Fabrication project update - COVID-19 edition
As terrible of a situation that the world is in right now, I’ve had at least one small silver lining. Since I’ve been stuck indoors with no possible plans, I’ve finally had time to bang out a few of the project ideas I’ve had in the back of my mind for a while. A silver lining, that is, until I got to the step of actually needing to build or machine them… Since I have no access to Pier 9 for the foreseeable future to complete them, I figured I’d at least toss up some pictures where I’m at with a few of my ideas. Who knows, maybe it’ll even keep me accountable to finish some of them.
Espresso tamp
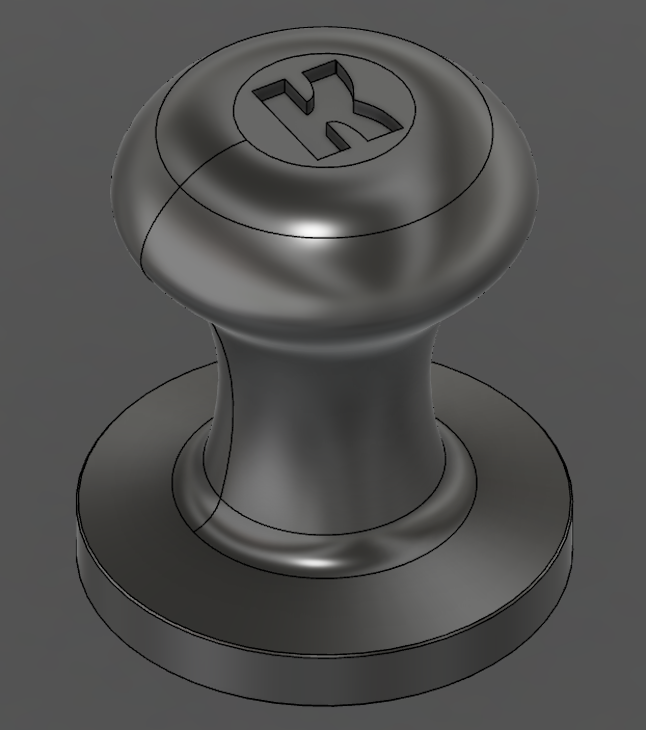
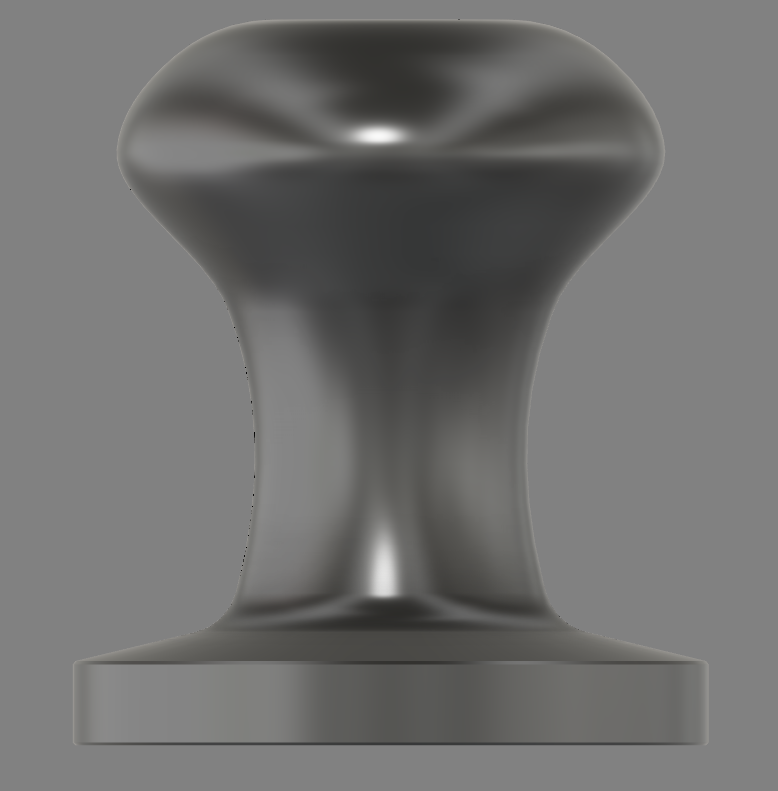
This one is fairly simple - my mom currently uses a cheap, plastic tamp that doesn’t even fit the basket correctly to make herself a latte every morning. Within the Pier 9 kitchen, there’s one that I could tell had been machined out of aluminum, so I figured this would be a fun gift. The Haas Lathe is one of the tools I haven’t learned yet so I didn’t want to start on the CAM for this one, but it seems like it would be a pretty quick setup to throw together.
Laser cut “record”
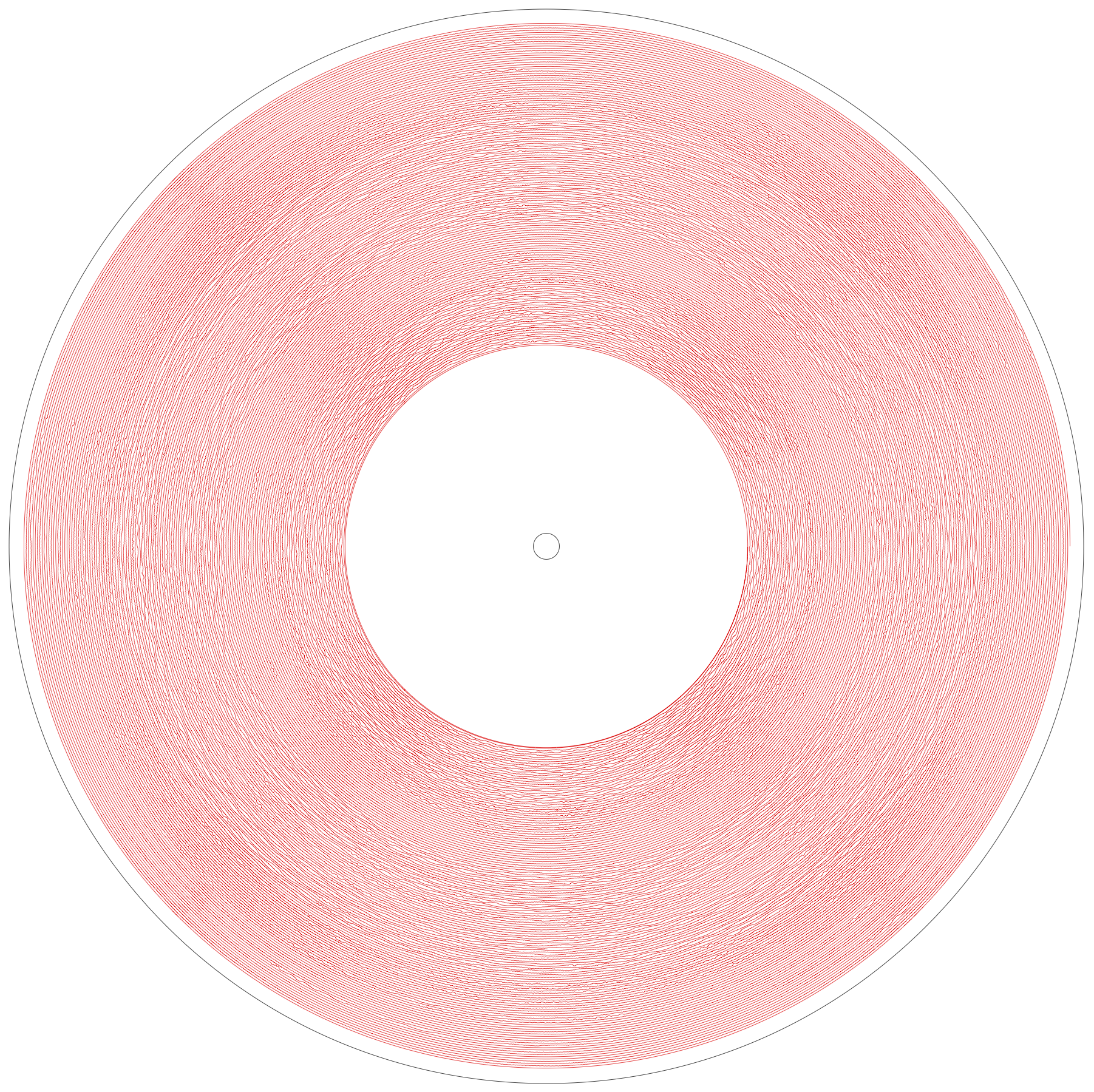
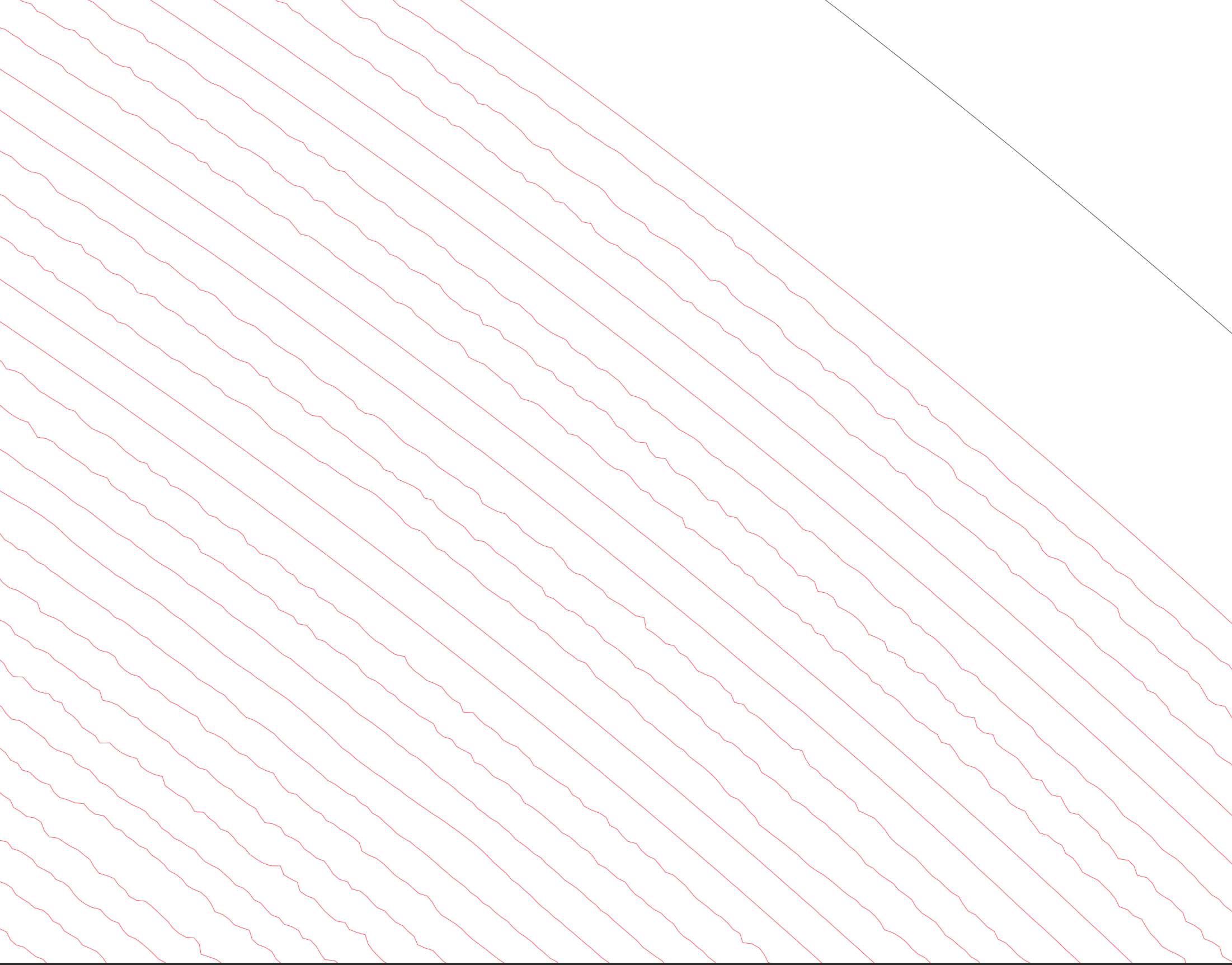
A closeup of the vectored audio waveform
I’ve made more progress on this! See the update here
I got the idea for this one after looking at some art people had done where they cut actual vinyl records into awesome images and text (like this). That idea was very quickly reconsidered when I found out that laser cutting vinyl produces chlorine gas and hydrochloric acid which don’t play well with human or machine (shocker).
Instead, I inverted the process in my mind - instead of cutting vinyl into other things, I could cut something else into the same semblance of a record. Turns out somebody already had the same idea (she’s a badass, check her out) and did all of the heavy lifting for me. She wanted to attempt to cut something that could be played on a turntable. I don’t need that fidelity, but something about being able to lasercut some wood squares with the waveform of some of my favorite songs and line them up anonymously on a wall appealed to me. I plan on playing with the code she wrote some more to produce different designs with audio waveforms rather than just a spiral.
Rippled wood designs
Right-click > Open in new tab for the full size images
The CAD stage showing the base waveform The CAM stage, with simulated toolpaths showing parallel toolpath grooves The CAM stage, with simulated toolpaths showing a combination of different toolpath grooves
This idea is a bit more out of my comfort zone than normal since it’s skewed further towards the art side of creating, versus something with function. The idea is that a dominant 3D waveform can be easily machined into wood (or another material), and usually the goal is to get it as smooth as possible. This is typically done by combining different toolpaths, like concentric, parallel, and others, along with a large tool radius. I thought it’d be interesting to go in the opposite direction and see how what secondary patterns I could create from the toolpath grooves.
I’m going to have to play with this a lot I think, but right now I have a couple basic sine(ish) waves running along the x-axis of the piece, and have indented it with multiple parallel toolpaths with a wide stepover. The plan is to start with a small-ish 12"x24" piece of 1" thick plywood and increase the dimensions as I get more confident in the designs.